For those that are interested, this is what the inside looks like of a 240ah lithium battery in a case.
There are 12 cells, connected to a 200ah BMS, it appears to be a Daly BMS, i didn't rip it completely out to see how its is wired as i wanted to test it to see how much AH it had after 3 and half years.
I charged it with the EBC-A20 charger/load tester, it only charges at 5 amp, so it took a few days

, but on the bright side, it appears the Passive cell balancing had a chance to do its job, as the BMS didn't activate during the load test after the charge was completed.
I was expecting the cells to show some loss of capacity, but to my surprise it had 240ah at 11.37 volts, i decided to end the test there as there would have only been 1-2% capacity left.
So I put it back in the van and did some more intense load testing at 90ah with the inverter, it seems that the battery cell that was causing an issue is now balanced and not tripping the BMS, so happy days
The only thing i didn't like with the the way the BMS is wired, is the 8AWG positive wire that is installed, It should have a more mm2 to carry 200Ah load, i'll install a larger cable when i take it out again.
I'll do some more load testing tomorrow to double check, but i'm glad that i managed to sort that issue out, there is a lot more life left in this battery.
But i can't wait until my new cells arrive so i can build my new bigger pack.
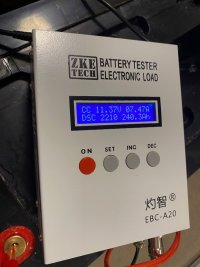