Hi,
I finally got to start this mammoth project today. The primary plan is to sound deaden my panel van as best I can as I take most of my business calls in it and lower road noise would help improve that. Secondary plan is to also insulate the rear (as a future proofing as I may use it as a day van kinda thing in the future). The van is only a month old. It was ordered without ply lining in the back so I could do this. I will also be plylining and then shelving the load bay for tool storage.
For the most part, my spec is going to be the same as in this video:
I started yesterday by emptying the van and foolowing a tip I'd read elsewhere, I marked where the raised ribs in the floor where. This is to enable screwing down of the 12mm ply I'm using for the floor. However, I don't like the idea of that so I plan so bond the ply to the top of the insulation...
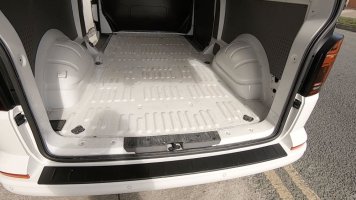
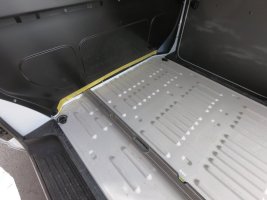
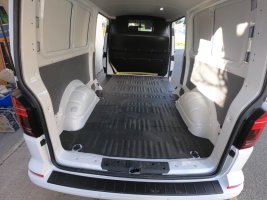
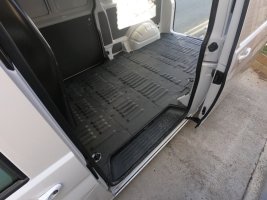
I'm planning to go out and begin creating a template for the 12mm ply floor that I am going to BOND to this dodo mat duo. I will cover the lashing rings as I never used them on my previous T6.
Does anyone have any thoughts on my decision to bond the ply down with a polymer adhesive (gun) as opposed to screwing down? I really ont like the idea of thowing a 100 screws through the metal floor to be exposed on the underside!
Adam
I finally got to start this mammoth project today. The primary plan is to sound deaden my panel van as best I can as I take most of my business calls in it and lower road noise would help improve that. Secondary plan is to also insulate the rear (as a future proofing as I may use it as a day van kinda thing in the future). The van is only a month old. It was ordered without ply lining in the back so I could do this. I will also be plylining and then shelving the load bay for tool storage.
For the most part, my spec is going to be the same as in this video:
I started yesterday by emptying the van and foolowing a tip I'd read elsewhere, I marked where the raised ribs in the floor where. This is to enable screwing down of the 12mm ply I'm using for the floor. However, I don't like the idea of that so I plan so bond the ply to the top of the insulation...
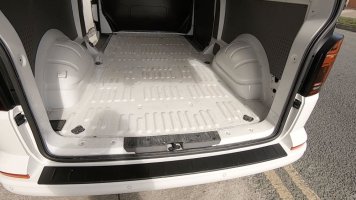
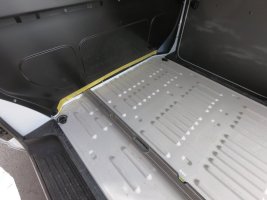
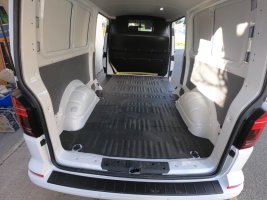
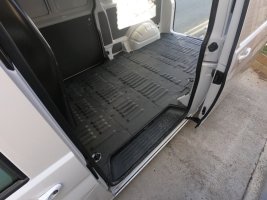
I'm planning to go out and begin creating a template for the 12mm ply floor that I am going to BOND to this dodo mat duo. I will cover the lashing rings as I never used them on my previous T6.
Does anyone have any thoughts on my decision to bond the ply down with a polymer adhesive (gun) as opposed to screwing down? I really ont like the idea of thowing a 100 screws through the metal floor to be exposed on the underside!
Adam